Workflow automation has become a key element in the digital transformation of companies, and if it's becoming increasingly widespread among supply chain players, it's for a good reason! Through the use of advanced technologies, organizations can reduce manual tasks, accelerate lead times, minimize human error and optimize the use of their resources. Here's how it works.
Automated document processing is the use of digital technologies and tools to automate and optimize the steps in a process or workflow. In other words, manual tasks usually performed by employees are carried out by ergonomic, easy-to-use software and computer programs.
By opting for a workflow automation solution, repetitive tasks are robotized, whether it's a single task or an entire process.
Ultimately, sales performance is boosted and team agility is enhanced. According to Salesforce, in 2021, 81% of organizations were already planning to automate part of their tasks by the end of 2022, using No-Code tools to create connected experiences. By this time, over 92% of French companies had already implemented or expressed a desire to integrate automation initiatives (Salesforce, press report on automation in France). However, the transport and logistics sector has not yet taken the plunge. Every year, more than 1.5 million man-days are lost due to manual data re-entry.
Moving to automated workflows offers clear advantages for all logistics structures (road haulage companies, freight forwarders, forwarding agents, warehouse managers, terminal operators, port authorities, shipping companies and other professionals in the field).
1. Reduce manual and time-consuming tasks
Automating logistics workflows reduces the number of time-consuming tasks requiring human intervention (data collection and entry, information transfer, sending follow-up e-mails, etc.). As a result, employees can concentrate on higher-value tasks.
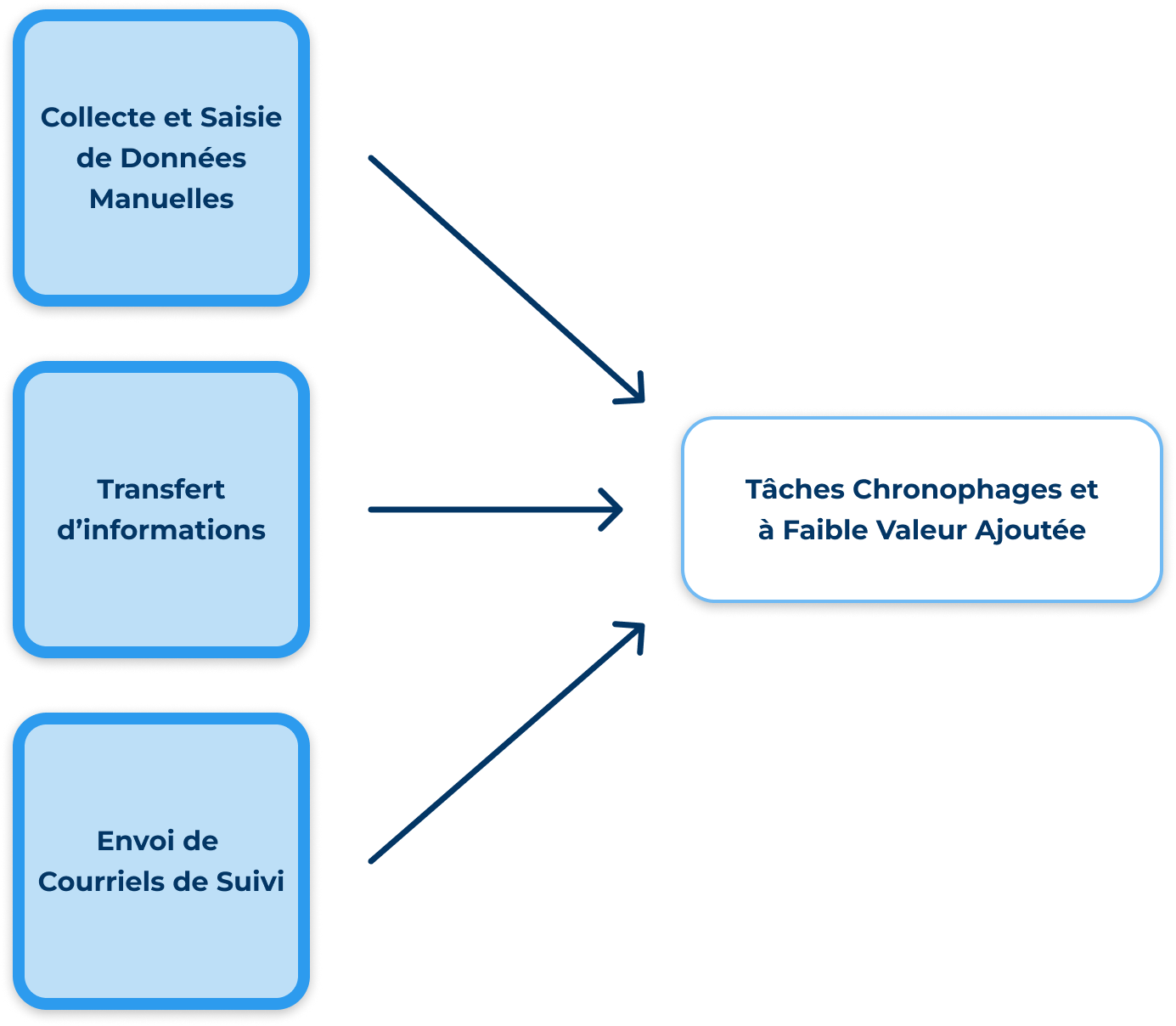
2. Better interoperability
In 2022, a study carried out by Talend showed that 97% of companies find it difficult to exploit their data due to long collection times and the poor quality of the data at their disposal. Yet many workflow automation systems are designed to improve and accelerate communication between different systems. With solutions like Docloop, you can easily connect the various application systems (WMS, TMS, ERP, etc.) used in your company and by your partners. The result: greater productivity and autonomy, and reduced error rates.
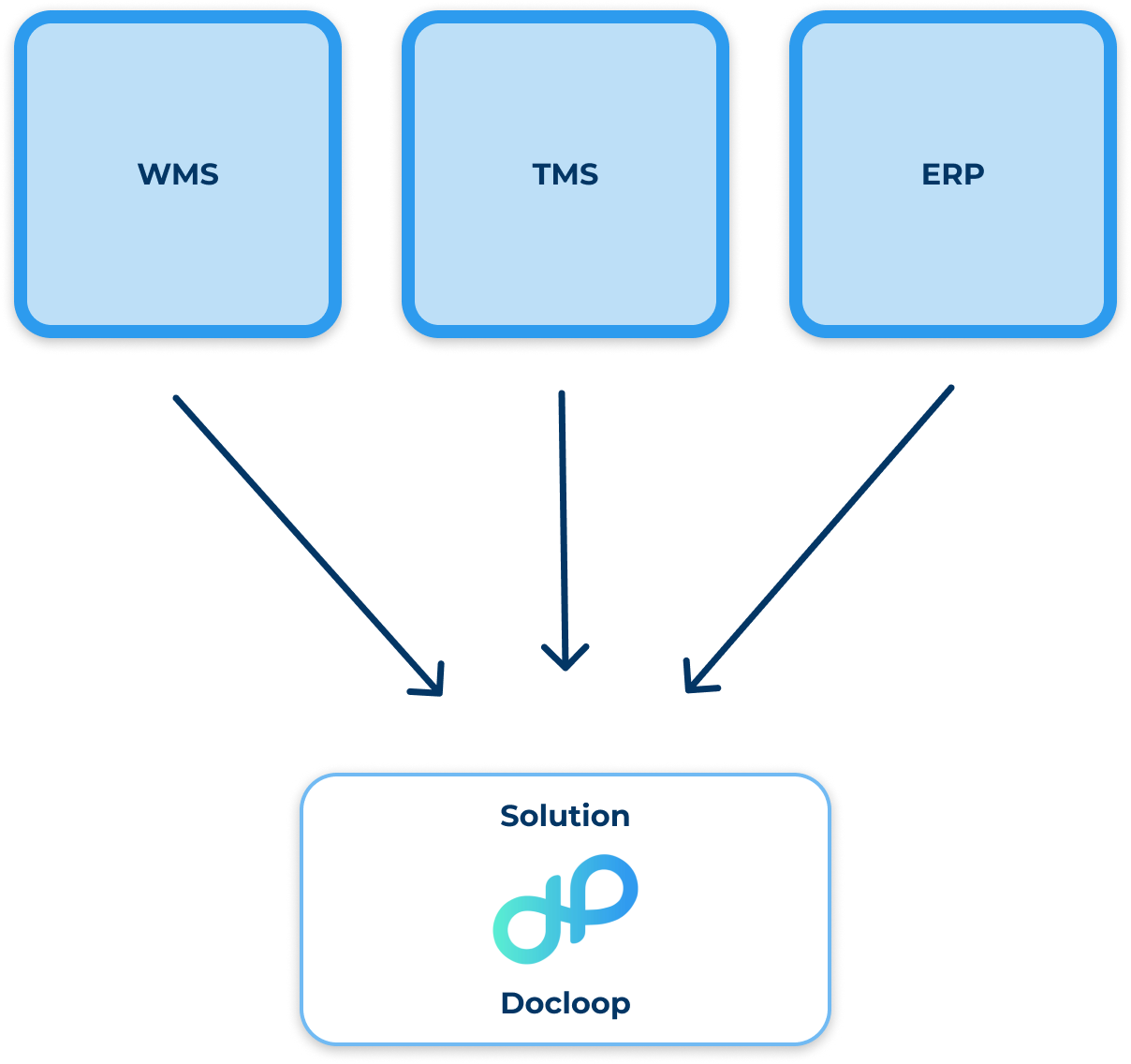
3. Simplified data extraction and structuring
By avoiding tedious manual tasks and providing fast, simplified access to key information, data extraction and structuring reduce data processing and management time. Choosing intelligent data processing is an excellent way of transforming unstructured information into organized, usable data.

4. Improve productivity by speeding up processes
Automated document management platforms like Docloop are key allies for logistics operators. The scenarios you create can be fed into your system 24/7, depending on the settings you have configured. The result is greater productivity and shorter processing times: automation could boost productivity by up to 30%! That's a record increase, and not a negligible one for any company.
By eliminating manual, tedious and repetitive tasks, your teams are more available and can concentrate on more rewarding tasks.
5. More precise exchanges, fewer data entry errors
Workflow automation systems help to increase accuracy by reducing human error. On average, an operator makes 1 error every 400 entries, compared with 1 in 1.5 million for an automation tool. This robotization ensures a better overview of the state of process performance, in real time.
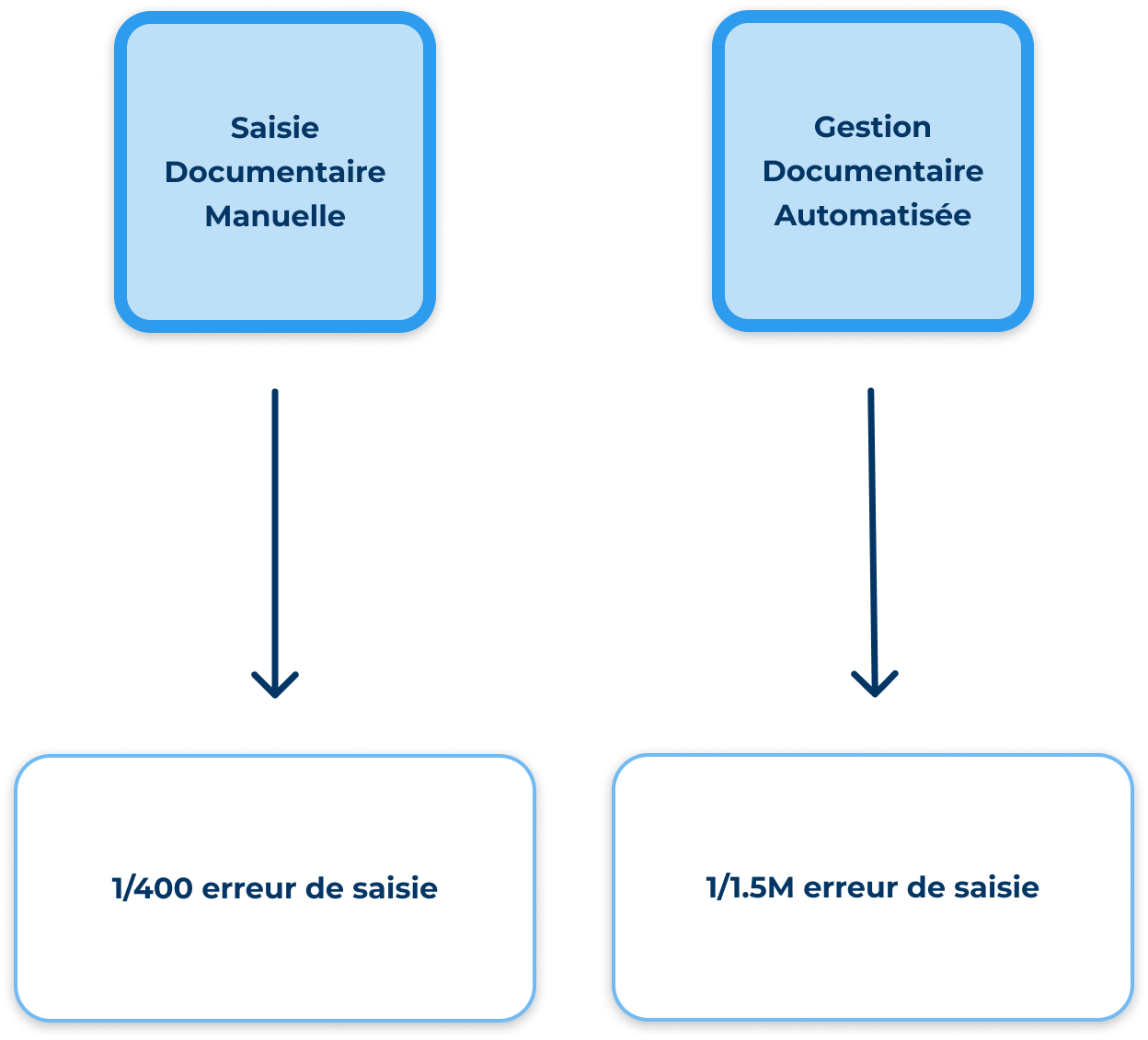
6. Optimizing resources
Automating workflows in a company leads to real optimization of resources. It streamlines processes, always eliminating repetitive steps and optimizing sequences of actions. For example, automated inventory management systems can help identify optimal stock levels and avoid costly over-stocking or stock-outs.
A study by McKinsey found that automating ordering processes reduced overall costs by up to 15% (Sales automation: The key to boosting revenue and reducing costs, McKinsey).
Similarly, the robotization of business processes can significantly reduce operational costs and labor-related expenses. Removing redundant tasks eliminates dependence on humans and certain tools to perform them.
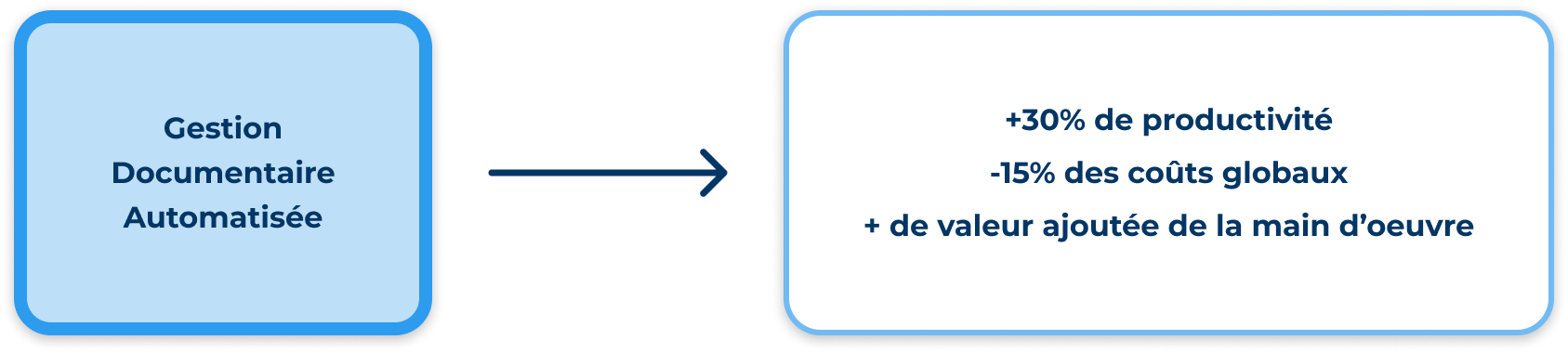
All the time. When tasks are repetitive, time-consuming and error-prone, automation is a solution to be seriously considered. It is also useful when processes involve numerous steps and coordination between different team members is difficult.
Automation can also be useful if your company manages large quantities of data or handles large-scale transactions. Automated workflow management tools are an option every company should consider.
While every industry has its own specific needs, workflow automation is particularly well suited to the supply chain. At Docloop, our functionalities have been designed to provide a quality solution for all players in the supply chain.
The benefits of automation are numerous (reduction of time-consuming manual tasks, improved interoperability between systems, simplified data extraction and structuring, faster processes and optimization of resources). But it's important to choose the right system for your needs, in order to implement effective automation.
In this context, Docloop is the ideal solution for all players in the supply chain. Thanks to functionalities designed specifically to meet the needs and problems of the supply chain, our intelligent document processing tool makes it easy to automate all or part of your processes, from automatic file opening to automatic invoice reconciliation, automated management of price lists and much more. What's more, with our infinite scenario editing system (loops principle), you can automate your various logistics processes, extract or transfer data, structure them better, translate them or enrich them, whatever the format (PDF, CSV, Excel, API...) or system (eFTI, eCMR, DCSA, B2P...).
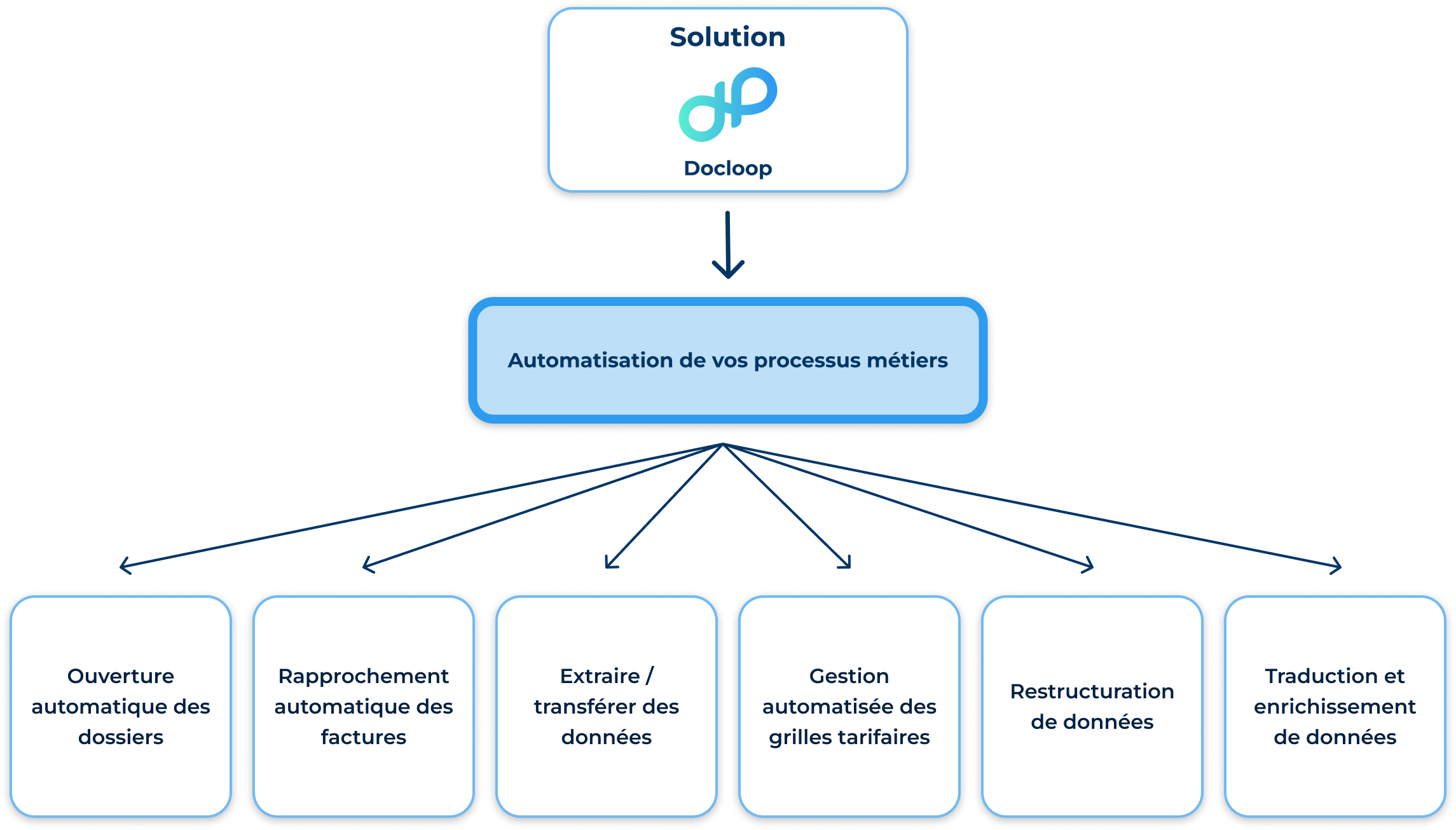
Other solutions do exist. WMS (Warehouse Management System), TMS (Transport Management System) or ERP (Enterprise Resource Planning) are alternatives that can help automate logistics workflows. However, unlike Docloop, these tools don't necessarily interconnect with the various services and software in your ecosystem.
Automating a workflow requires a certain amount of preparation. First and foremost, it's essential to analyze and understand your company's current processes to find the right solution. Once this is done, there are a few steps you should not overlook:
- Identify the flows that need to be automated: repetitive tasks, actions where errors are frequent... Prioritize the areas where automation can bring the most value. To do this, you can take into account employee experience.
- Use the right tools: select the solution best suited to your needs. Also remember to choose a tool that integrates seamlessly with your existing systems.
- Testing: carry out thorough tests to ensure that the automation works as intended. Correct any errors or problems before final integration.
- Train employees: before implementing automation, it's important to train the users and employees affected by the new automated workflow.
- Set up the automation: all that's left is to deploy the automation system within your company. Don't forget to regularly monitor its operation and collect feedback from its users to adjust it as quickly as possible.